44起!化工工艺典型事故案例统计与分析研究(2001-2024)
2025-03-15 本站作者 【 字体:大 中 小 】
【编者按】化工生产贯穿了危险化学品原料采购与储存、生产以及最终产品的全过程。根据安全保护层理论,工艺设计则是安全保护层的核心,它能够从源头上消除化工工艺事故发生的可能,是实现本质安全的关键所在。着《化工过程安全管理导则》(AQ/T 3034)的更新修订,过程安全管理要素提升至20个,覆盖了从安全基础管理、本质安全设计、关键操作、专业管理、重点环节、本质安全提升和持续改进。任何工艺事故均能在过程安全管理里找到“症结所在”,落实过程安全管理使得事故隐患更是无处遵循。
中国石油和化学工业联合会安全生产办公室组织行业安全专家进行了专题研讨,梳理了2001-2024年的化工工艺典型事故案例,通过诊断化工过程安全管理的“症结”,给出了风险防控措施建议,供业界参考。
一、化工工艺类典型事故案例汇总
二、典型事故综合分析
据不完全统计,本专题收集了2001年11月-2024年8月,国内外化工类企业在生产期间发生的44起一般及以上化工工艺典型安全事故(含1起美国事故),分别从事故等级(含死亡人数)、事故类别、作业环节和原因类别等四个方面进行了综合分析,然后结合具体案例进行详细分析,得到以下结果(因统计事故数据基数有限,分析结果存在一定偏差,仅供参考):
(一)事故等级(含死亡人数)
本次统计分析一般及以上事故的事故等级(含死亡人数),如下表所示:
从上述统计数据可以看出:工艺类事故等级主要为较大事故,高达51.16%,而在死亡人数方面,重大事故和较大事故占比分别高达56.95%、37.22%。装置自动化程度低或因工艺特点导致现场操作人员密集,同时部分企业因从业人员素质参差不齐,现场操作处置不当和现场管理不到位等多重因素叠加导致群死群伤的概率增加。
(二)工艺类事故类别分析
统计分析的事故主要集中在爆炸、火灾和中毒窒息事故三类,如下表所示:
工艺类事故类别分析
事故类别
数量
占比
死亡人数
占比
爆炸
35
79.55%
191
85.65%
火灾
11.36%
25
11.21%
中毒窒息
9.09%
3.14%
合计
44
100.00%
223
100%
从事故类型来看,爆炸事故占统计事故类型总起数的79.55%,死亡人数占比高达82.65%。这些数据与危化品生产或储存企业的原料或产品易燃易爆,生产装置和化工工艺过程危险系数高的特点密切关联,爆炸是造成人员群死群伤的主要原因。
(三)工艺类事故作业环节分析
统计分析的事故包括投料、开车、现场操作、指标调整、停车和其他等环节的数据,如下表所示:
工艺类事故作业环节分析
事故类别
数量
占比
现场操作
18
40.91%
投料
11
25.00%
指标调整
15.91%
开车
6.82%
停车
2.27%
其他
9.09%
从上图可知,现场操作、投料和指标调整是导致工艺类事故发生的主要环节,占比分别为40.91%、25%、15.91%。现场操作是化工生产的日常主要工作之一,受到员工的责任心、业务技能水平与操作经验等方面的综合影响。而投料环节直接影响物料的反应,原料纯度、投料程序与条件确认(如配比、温度、压力和速率等)是决定工艺安全与否的开始。指标调整包括但不限于对日常指标,异常工况的处理,是过程安全管理的核心因素之一。
(四)事故主要原因统计分析
本次统计分析主要按“三违”管理缺失、设计不合理、风险辨识不到位、误操作、设备缺陷、异常工况处置不当、应急处置不到位、危险化学品管理混乱、防爆管理不力、变更管理不到位、交接班管理不严格等常见原因进行统计,如下表所示:
工艺类事故原因分析统计
原因分析
数量
占比
“三违”管理缺失
23
30.67%
设计不合理
14
18.67%
风险辨识不到位
12.00%
误操作
8.00%
设备缺陷
8.00%
异常工况处置不当
8.00%
危险化学品管理混乱
4.00%
应急处置不到位
2.67%
防爆管理不力
2.67%
变更管理不到位
2.67%
交接班管理不严格
2.67%
合计
75
100.00%
从事故发生的原因来看,“三违”管理缺失、设计不合理、风险辨识不到位为最主要的三个因素,分别为30.67%、18.67%、12%;误操作、设备缺陷、异常工况处置不当“平分秋色”,均为8%。因风险辨识不到位使得认知不足,违章作业或操作随意性强导致事故频发;因工艺、设备和电气仪表等设计选型不合理等因素导致后期生产处于被动局面,各专业之间的相互影响最终在工艺类事故中得以集中体现。同时,操作人员个体差异(如责任感、经验、应急能力、安全素养等)导致员工存在误操作、异常工况处置能力不足。
三、典型事故技术分析
本专题主要从“三违”管理、工艺本质安全、风险辨识、异常工况处置、安全信息管理、人员和变更等方面进行分析。
(一)“三违”管理缺失。
员工违反工艺操作规程,未按规程要求进行投料、操作、控制反应指标,导致反应失控发生事故。重庆市长寿县长风化工厂“11•7”二苯甲酮工段泄漏爆炸事故是由于操作人员未按工艺要求操作,在温度偏低时加入过量光气所致。镇海炼化“5·3”火灾事故主要原因是违反操作规程,没有对流程线有关阀门进行检查确认就进行引油作业。重庆紫光国际化工有限责任公司“9·25”中毒窒息事故是由于中控室操作进行2号成盐反应釜加入反应物料时,违反《成盐岗位操作规程(试行)》,未将电机频率调回至要求的规定范围,使釜内物料反应不均匀,导致釜内温度过高、反应失控,最终发生爆沸。
(二)工艺的本质安全管理重视不够。
1、在役化工装置未经正规设计,致使工艺流程设计缺陷,自动化控制系统缺失或失效。
重庆长风化工厂“11•7”二苯甲酮工段泄漏爆炸事故直接原因之一是由于未设置成盐釜搅拌电机频率、电流与氢氰酸加料控制阀之间的联锁装置;江苏连云港聚鑫生物科技有限公司“12·9”重大爆炸事故中,装置生产过程整体自动化控制程度存在严重缺陷,间二氯苯成品精馏、残液精馏等设备仅设置单一温度显示仪表,缺乏超温报警及调节控制设施;开远市龙腾冶炼厂“3·23”煤焦油储罐火灾事故则是由煤焦油储罐设计不规范(顶部未设置呼吸阀)引起;辽宁众辉生物科技有限公司“5.26”一般爆炸事故”的直接原因之一是“放料管线没有设置完整的静电导出设施,流体与内衬四氟的管壁摩擦产生的静电汇集至放料管口,电荷达到极限放电产生火花引爆了釜内爆炸性混合气体”。
2、未按工艺设计采购、安装设备设施,改变设计条件,降低了设备性能,造成设备隐患。
腾龙芳烃(漳州)有限公司“4•6”爆炸着火重大事故中,焊口存在焊接质量问题的管道受开工引料操作波动引起的液击冲击而断裂,引发了事故。美国俄亥俄州涂料企业“4·8”火灾事故是由于安装在反应釜上的爆破片(设计压力为105.5-117.2kPa)与工艺安全要求的压力范围(93.1-103.4kPa)不一致。操作人员重启搅拌时高温物料挥发超压而爆破片没有启动爆破泄压,树脂与石脑油的混合物从反应釜的人孔泄漏导致爆炸并引发了火灾事故。
3、随意变更工艺设计,不尊重本质安全设计。
锦州市鑫泰基精细化工有限公司“5·12”爆炸着火事故是因事故单位对已建成装置违规改建,擅自改变原设计的生产工艺、原料、设备管线及生产用途造成的。
(三)风险辨识不到位。
山东国金化工厂“8·25”较大爆炸事故是由于对长期停车后复工环节,对于装置中氢化塔内钯催化剂及其滤网未更换,开车后系统内杂质较多而引起的。浙江华邦医药化工有限公司“1•3”较大爆燃事故是由于当班工人擅自加大蒸汽开量且违规使用蒸汽旁路通道,致使主通道气动阀门自动切断装置失去作用,最终导致反应温度失控引发爆炸。聊城鲁西化工“5·1”重大爆炸着火事故是由于操作人员抽取的70%双氧水表面漂浮物时与原工作液配制釜内原存有的氧化液、地沟工作液中含有氧化铝粉末、钯催化剂粉末、灰尘等杂质发生反应所致。
(四)异常工况应急处置不当。人员培训不到位,缺乏异常工况判断能力和应急处置能力不足,导致事故发生或扩大。
盐城氟源化工有限公司临海分公司“7.28”爆炸事故是由于在氯化反应塔冷凝器无冷却水、塔顶没有产品流出的情况下没有立即停车,而是错误地继续加热升温,使物料(2,4-二硝基氟苯)长时间处于高温状态并最终导致其分解爆炸。沧州大化TDI有限责任公司“5·11”爆炸事故是由于硝化系统在处理系统异常时,酸置换操作使系统硝酸过量,甲苯投料后导致一硝化系统发生过硝化反应所致。盛华化工公司“11·28”重大爆燃事故因操作人员没有及时发现氯乙烯气柜卡顿并引发的物料泄漏,仍然按照常规操作方式调大压缩机回流且调节幅度过大,氯乙烯冲破环形水封泄漏向厂区外扩散遇火源所致。自贡富顺西艾氟科技有限公司“5·3”较大爆炸事故是员工在反应出现异常后盲目进行处置,未认真分析原因就擅自加大催化剂投放并引入蒸汽加热,导致四氟乙烯爆聚引发合成反应釜爆炸。
(五)安全生产信息管理缺失,危化品管理不到位。
1、包装标识不到位。
宜宾恒达公司“7·12”爆燃事故的直接原因是由于员工投料时,将无包装标识的氯酸钠当作丁酰胺使用而导致。辽宁先达农业科学有限公司“2•11”爆炸事故是由于在烯草酮生产投料环节,一操张X未对物料进行复核确认、二操杨XX错误地将丙酰三酮与氯代胺同时加入到氯代胺储罐V1428内导致发生爆炸事故。
2、危化品物料管理混乱。
湖南冠元生物科技有限公司“5·17”爆炸事故主要原因是由于企业违规在车间内存放大量桶装乙醇,爆炸发生后车间内桶装乙醇大面积外溢流淌并受高温烘烤蒸发,爆炸后车间内燃烧猛烈导致受困人员不能有效逃生。
(六)人员不具备化工生产的专业技能、安全素养或责任心缺失,导致违章作业频繁发生。
1、人员不具备化工生产的专业技能。
河北克尔化工有限公司“2·28”爆炸事故,从业人员不具备化工生产的专业技能,对工艺理解不透,处理异常情况能力低,擅自将导热油加热器出口温度设定高限由215℃提高至255℃,使反应釜内物料温度接近了硝酸胍的爆燃点(270℃)。
2、责任心或安全素养缺失。
阳煤丰喜肥业公司临猗分公司“8·31”煤气中毒事故的原因是企业在导淋排液过程中现场作业人员擅自离岗,无人监护,排液阀长时间未关闭造成大量粗煤气排出。安徽省安庆市鑫富化工有限公司“3•27”爆炸事故是由于当班操作工误操作,误将甲醇高位槽阀门打开,将用于洗釜的高位槽剩余甲醇代替二甲基甲酰胺加入到釜内引发剧烈反应所致。宜昌富升化工有限公司“2·19”爆燃较大事故是由于操作人员对温度偏高(190℃~201℃),未按岗位操作规程要求“超过工艺指标(150℃~175℃)采取加水降温的措施”所致。
(七)变更管理未有效执行,未进行充分小试、中试等实验、论证、分析,盲目改变。
广西玉林"10·15"较大爆炸事故是由于技术负责人将分4次加入NaOH水溶液的方式,擅自改变为分2次投入固体NaOH所致。
四、防控措施建议
针对事故案例原因的统计与分析,现从工艺纪律管理、工艺路线选择、本质安全源头设计和生产运行管理等方面提出以下建议:
(一)建立并落实安全生产管理制度,杜绝“三违”,严肃工艺纪律。
1、建立并落实工艺管理制度。根据88号文、AQ/T3034等法规与规范要求,建立至少覆盖安全生产信息管理制度、风险管理制度、操作规程管理制度、开停车安全条件检查确认制度等制度。明确各专业管理部门的职责、管理程序和激励措施等要求,对落实情况定期开展审核。
2、严禁违章指挥、违反劳动纪律、违章操作的行为。企业应将严禁违章指挥、违反劳动纪律和违章操作,将“三违”作为不可逾越的安全管理红线并进行更为严厉的处罚。
3、加强对工艺纪律的考核。对工艺指标的控制进行严格管理,制定合理的控制范围,严禁工艺指标控制超标、大幅度调节和随意私自变更等行为。
4、加强对工艺报警、联锁的管理。操作人员必须及时响应装置所有报警,第一时间进行现场确认,严禁不分析原因、不到现场确认就随意消除、屏蔽等行为,装置联锁触发后应及时查明原因,并逐一消除联锁触发条件,严禁强行复位。紧急处置时,企业未开展评估和进行审批,不得摘除或旁路联锁以强制维持设备或装置运行。对于因设置不合理确需要进行变更的,应严格执行变更程序。
(二)重视工艺路线的选择,工艺技术来源的合法性与可靠性。
1、做好工艺路线选择政策符合性。结合所在地区的产业发展定位和危险化学品“禁限控”目录、淘汰落后危险化学品安全生产工艺技术设备目录(包括第一批、第二批)等进行工艺技术与设备的选型,选择来源合法、安全可靠的工艺技术。
2、做好反应风险评估,确保技术的可靠性与合法性。尚属首次国内首次使用的工艺,按规定进行安全可靠性论证。精细化工项目应按规定进行反应安全风险评估,并确定反应工艺危险度等级。
(三)落实本质安全源头设计
1、危险化学品建设项目要严格落实安全预评价与安全设施设计。确保评价单位、设计单位和施工单位资质符合要求并规范设计与施工,符合“三同时”的要求;在初步设计阶段开展危险与可操作性分析(HAZOP 分析),并在设计中进行落实。
2、落实“两重点一重大”建设项目设计要求。
重点监管的危险化工工艺:严格按照重点监管的危险化工工艺安全控制要求、重点监控参数及推荐的控制方案进行工艺设计。重点监管的危险化学品:按照重点监管的危险化学品安全措施和应急处置原则要求,落实应急处置、防范措施、应急器材和个体防护装备配备的有关设计要求。重大危险源:落实危险化学品的重大危险源辨识和分级,落实监测监控系统、应急救援器材和设备配备的有关设计要求。
3、推进安全工艺技术设备更新升级,实现自动化减人。建设项目应满足法律法规、规章及标准规范关于自动化系统装备建设的要求,实现现场无人操作或最大程度减少现场作业人员数量。如涉及硝化、重氮化、过氧化、氟化、氯化等高危工艺装置在规定时限内完成微通道、管式反应器等新装备、新技术应用,上下游配套装置应实现原料处理、反应工序、精馏精制和产品储存(包装)等全流程自动化。
4、加强对在役装置的安全设计诊断复核。企业根据应急管理部办公厅关于印发 2023 年危险化学品安全监管工作要点和危险化学品企业装置带“病”运行安全专项整治等9个工作方案的通知(应急厅[2023]5号)附件5之附件2《危险化学品企业安全设计诊断复核指南》并结合所在地区具体要求,开展安全设计诊断复核工作。
(四)加强生产运行管理
1、制定完整且实用的岗位操作规程。一是要确保内容的完整性。企业结合实际情况且确保内容符合AQ/T 3034-2022 4.9.1操作规程要素要求。二是确保操作规程内容可操作性与持续更新。操作规程应及时反映安全生产信息、安全要求和注意事项的变化。三是狠抓操作规程的执行与落实。企业可考虑通过经济措施或管理措施对违章操作进行严厉打击。
2、重视公司重点人群,提升业务技能。
1)重视公司重点人群与安全管理机构的合法合规性管理。主要包括以下方面:(1)涉及“两重点一重大”危险化学品生产建设项目的企业,主要负责人和分管生产、设备、技术、安全的负责人及安全生产管理人员学历与职称要求。(2)涉及重大危险源、重点监管化工工艺的生产装置、储存设施操作人员和涉及爆炸性危险化学品的生产装置和储存设施的操作人员学历要求。(3)安全生产管理机构的设置和专职安全生产管理人员、注册安全工程师的配备比例。(4)特种作业人员、特种设备作业人员、消防设施操作员等须持证上岗。最后,针对上述相关人员要按规定每年定期开展再教育培训。
2)企业内部工艺培训,应考虑从以下方面开展:
(1)抓好阶段性培训。项目建设后,使操作人员在上岗前先接受规范的基础知识和专业理论培训。装置试生产前,企业要完成全体管理人员和操作人员岗位技能培训,确保全体管理人员和操作人员考核合格后参加全过程的生产准备。装置运行期间,着重员工对正常操作、临时操作的操作技能培训,做好异常工况的判断与处置并定期开展培训。
(2)强化岗位员工安全职责培训与安全习惯的培养。规范上岗考核和年度岗位能力考核,尤其是装置预防性调整和应急处置能力,避免高分低能,确保操作人员达到岗位所需的技能和工作态度。同时,加强对员工日常安全行为的考核,让一线员工养成良好安全习惯。
3)强化本岗位员工的应急处置能力。一是开展应急演练强化岗位员工对异常工况的判断与处置。二是通过应急物资或装备使用培训,提高个人防护与自救、互救能力,加强团队协作,综合考虑环境保护和个人职业健康等方面的应急处置,避免顾此失彼。
3、规范生产装置开停车管理。
1)重视开车的组织机构,保证开停车严肃规范。成立开停车组织机构,明确各岗位、各专业的管理职责并做好应急处置。
2)做好装置试生前的各项准备工作。针对首次开车的情形,确保严格按照“三查四定”、系统吹扫冲洗、气密试验、单机试车、联动试车、投料等环节的要求逐步推进,逐项发现、消除各类隐患,做好投运前安全检查(PSSR)、试生产方案审查等关键工作,对于开车前必改隐患做到“未整改到位绝不开车”。
3)开停车过程管理。企业要制定开停车安全条件检查确认制度,做到步步有落实,步步有确认。企业要落实开停车安全管理责任,严格执行开停车方案,建立重要作业责任人签字确认制度。重视配套安全措施、环保措施、消防设施和职业卫生保障措施。
4、强化变更管理。
1)严格变更管理。按照88号文要求,各企业应结合实际情况梳理明确工艺技术变更、设备设施变更和管理变更范围。
2)严格履行变更管理程序。各企业严格执行申请、审批、实施、验收等各环节管理要求,严禁私自变更或未按规定程序实施变更,可参照《化工企业变更管理实施规范》(TCCSAS 007-2020)并结合企业实际情况开展。
5、加强物料管理。
1)外购危险化学品入库管理和生产领用管理。必须确保物料包装完好无损且“一书一签”信息准确。做好物料的出入库、领用等环节的台账管理,存放管理严格按照《危险化学品仓库储存通则》、管制类化学品按相应技术规范或要求落实。
2)做好仓库管理。在生产装置的中间仓库,特别是对于甲、乙类物品中间仓库,做好领料的数量控制(大量使用时,不得超过一昼夜的储量)与现场临时存放管理,严禁超品种、超量储存,混放等情况。
3)严格做好废旧包装物和剩余物料的管理。对于附着危险物品的包装或包装物内的剩余物料,做好登记、标识做好退库或再使用等环节的管理,严禁使用未经确认的包装物或未经充分清洗置换的包装物。
6、加强应急处置能力建设,提升异常工况管理能力。
1)开展装置异常工况的风险辨识与处置能力培训与宣贯、演练。一是培训员工的异常工况判断识别能力与风险辨识能力。如针对工艺指标偏离的判断、现场运转设备运行异常的检测、远传液位计显示漂移的识别等均要明确判定标准,确保标准可量化与可操作性。让员工认识到工艺指标的持续偏离会引发物料分解爆炸、物料泄漏、导致人员中毒等严重后果。
二是要提升员工异常工况的处置能力。掌握工艺指标偏差后果和处置措施,熟悉设备倒换、漏点处理、物料堵塞、动设备启停等应急处置要求,保证在出现异常工况时,确保处置过程响应迅速且精准高效。
三是制定应急预案并定期开展演练。重在检验并完善应急预案的实用性与可操作性,加强公司内部管理层与基层班组之间、现场实操与中控人员操作之间、上下游装置之间、各专业之间、关联企业之间的衔接。
2)建立完善岗位人员紧急停车、人员撤离等授权机制。企业结合实际情况,明确紧急停车和人员撤离授权流程,撤离操作规范(至少包括撤离路线规划、撤离指令传达、撤离纪律要求、个人防护用品使用和特殊区域撤离要求等),确保在即使在节假日或夜间,异常工况都能有序指挥与高效应急。
7、重视设备管理,杜绝带病运行。
1)开展设备的预防性维修或保养。关键设备要装备在线监测系统。要定期监(检)测检查关键设备、连续监(检)测检查仪表。严格落实设备维护保养或定期更换,及时消除各类安全隐患。
2)加强动设备管理。企业要编制动设备操作规程,确保动设备始终具备规定的工况条件。自动监测大机组和重点动设备的转速、振动、位移、温度、压力、腐蚀性介质含量等运行参数,及时评估设备运行状况。加强动设备润滑管理,确保动设备运行可靠。
8、吸取事故事件的教训,对标过程管理要素持续提升。
企业要加强对工艺相关的事故管理。事故(含未遂事件)至少包括生产事故征兆、非计划停车、异常工况、泄漏、轻伤等。排查事故事件的根本原因,并在事故(事件)调查后,制定并落实针对性防范措施。同时更要密切关注并学习同类型企业的事故案例并吸取教训,对照本企业进行类比排查,弥补本企业过程安全管理相应要素的短板。
企业应定期开展以过程安全管理审核为主要内容的审核,包括工艺、设备、电气、仪表、公用工程等相关专业。逐一排查并解决过程艺安全管理的各类隐患,补齐短板,真正提升装置工艺安全管理水平。
(五)结论
通过对典型化工工艺事故的分析研究表明,化工工艺事故有其系统性与复杂性。只有抓住工艺路线选择与本质安全源头设计这个“根”,严格抓好工艺纪律,操作规程的执行,变更管理、人员培训、异常工况处置、物料管理与设备管理这些“杆”,工艺安全管理才会“枝繁叶茂”,工艺管理水平才会有实质性的提升,为化工企业良性发展提供安全保障。希望本研究能为从事化工生产相关工作人员及其他安全工作人员提供有益的参考和借鉴。
以上供参考。
水平有限,欢迎补充完善。
出品:中国石油和化学工业联合会安全生产办公室
整理:曾金、李光明、孙玉龙、王月明、陈涛、范志涛

猜你喜欢

喜报|恭贺综路传媒荣膺2017年度“最佳服务奖”!


南京中脉科技涉嫌传销 今年多地曝光


陕西杨凌:瞄定“产业高地”目标 打造百亿级产业集群


“我想对您说!”番禺区委书记会场上5次喊话企业家投资番禺


三星笔记本电脑怎么连接无线网wifi 三星笔记本电脑怎样连接无线网wifi


BOILER ROOM锅炉房蒸汽弥漫到北京电子城市


我国最神秘的十所大学,第一名非985、211,第二名人称“官校”


怎样分析与快速维修液晶电视机原理与故障


10轮融资,5G+AI,无人机链主企业因诺科技IPO冲刺


深圳市发展和改革委员会


Surface RT与新iPad,到底谁的显示效果更好
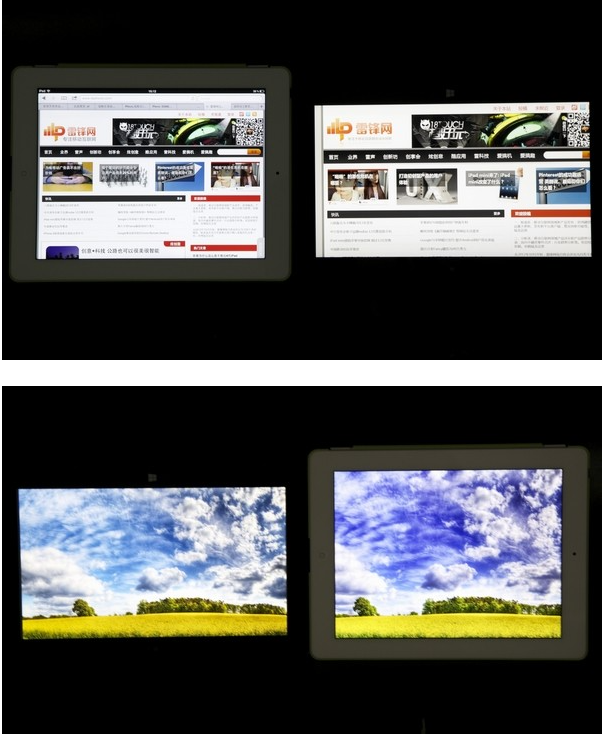

手机连不上wifi是怎么回事 手机连不上wifi是什么情况


京东白条怎么用 京东白条怎样用
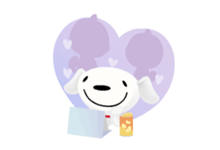

wifi拒绝接入是什么意思 wifi拒绝接入的意思是啥
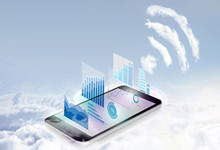

网速和网线有关吗 网速和网线有没有关
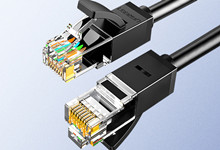